The Midwest currently boasts some of the lowest energy rates in the country, but that hasn’t stopped forward thinking utilities and power producers from moving ahead with energy storage projects that will support them in the transition to clean energy. We’re on location at one such FlexGen project in Indiana, where the site is a hive of activity.
Let’s walk through some of the highlights to building a Battery Energy Storage Project with the help of some images taken at the project site as it progresses.
First, we start with the “dirty” work. The site has to be cleared and graded to prepare it for the underground conduit and concrete pads that will hold the battery enclosures.
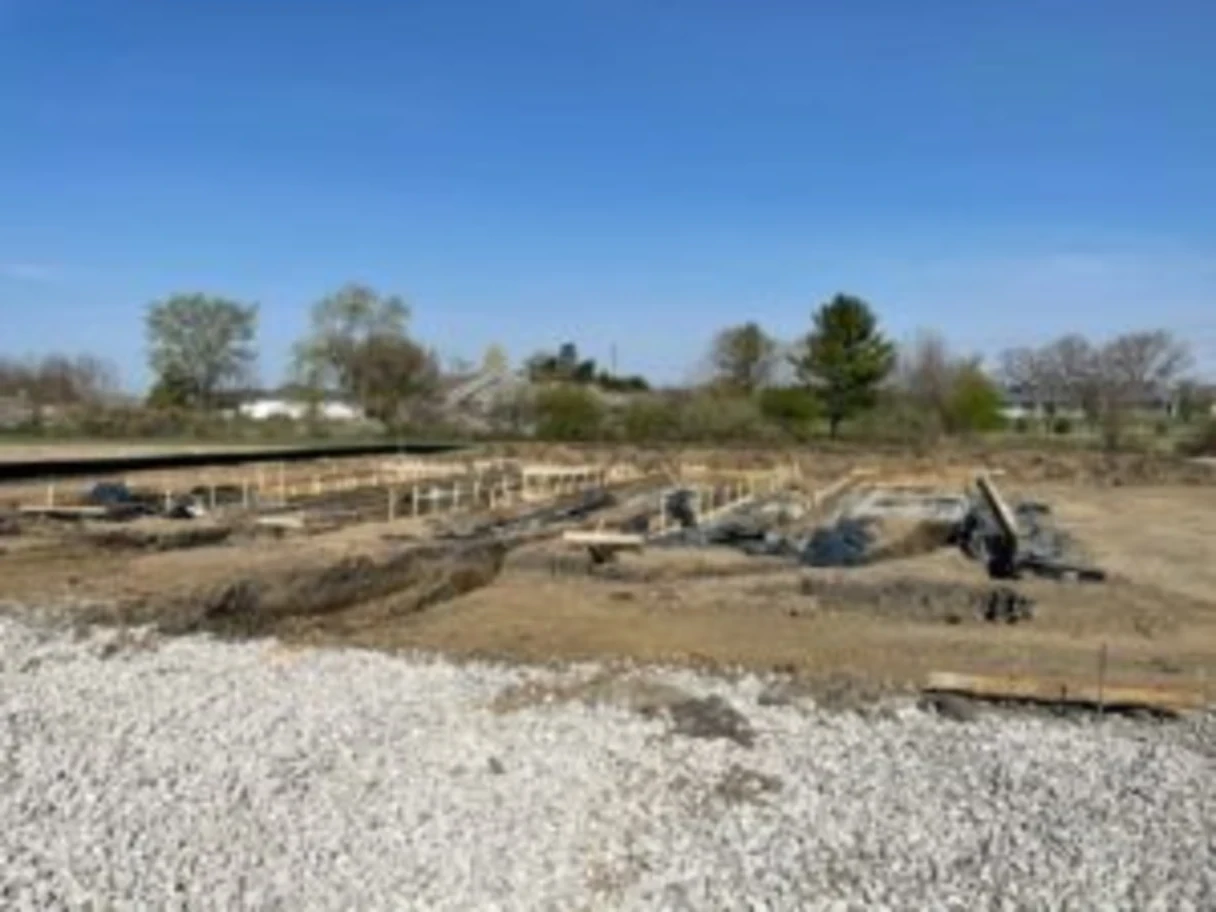
Second, the site design begins to take shape as the wood and rebar framing is laid. This is the outline to each of the future concrete battery pads.
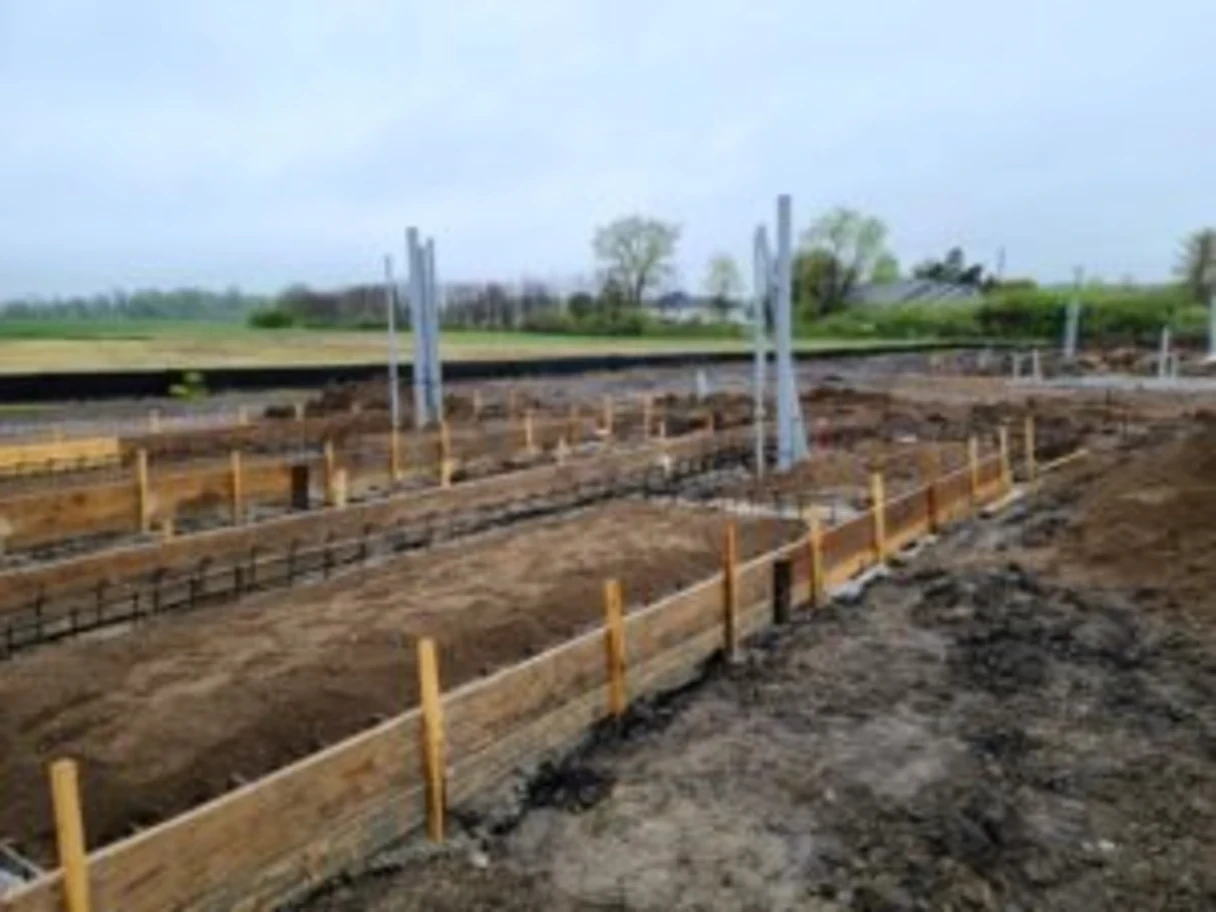
Third, we see the underground conduit that will connect the batteries being pulled and stubbed, this will allow for the coupling of the wires below the grade of concrete to keep future extensions of the conduit from protruding beyond the top of the concrete pad.
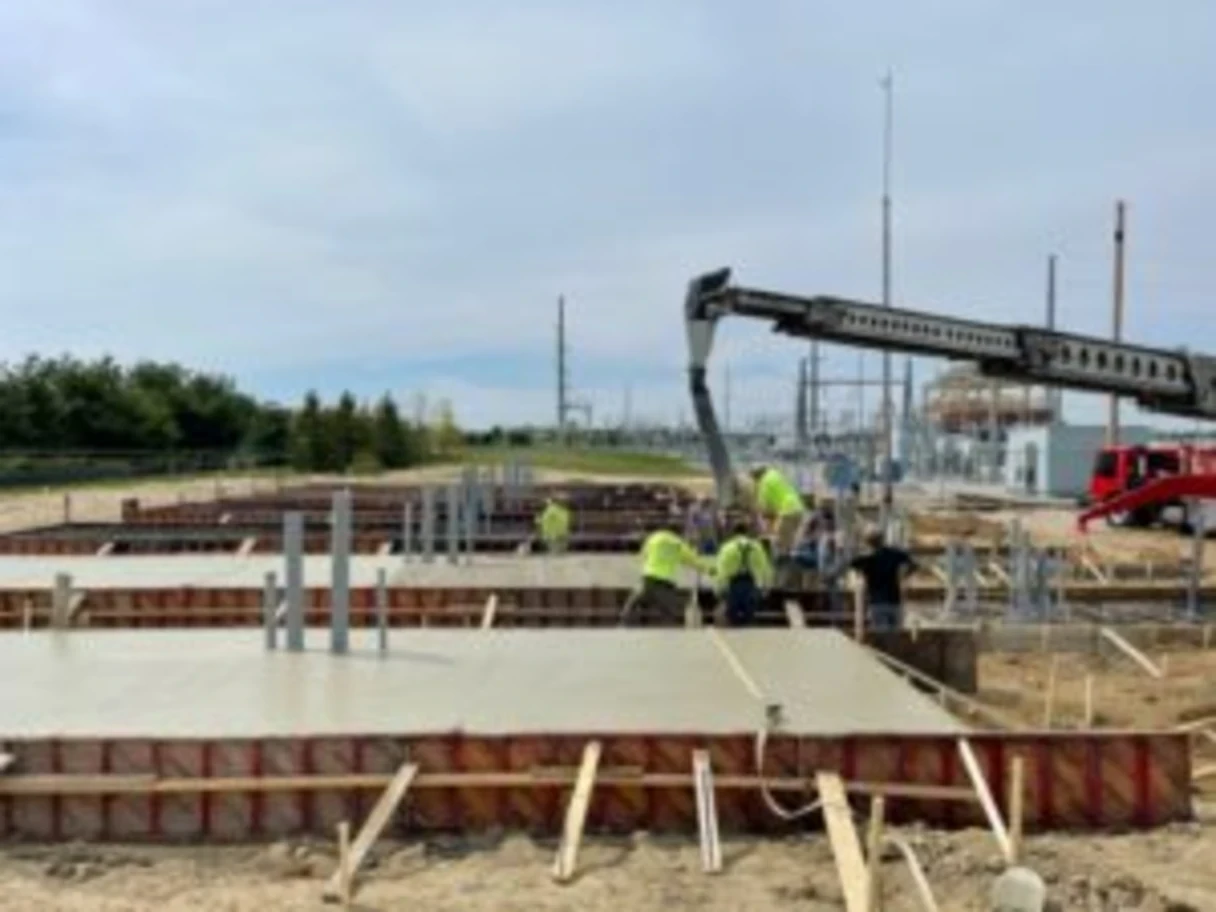
Here the site crew is pouring the concrete that will form the 6 main pads that hold the batteries…that’s a lot of concrete!
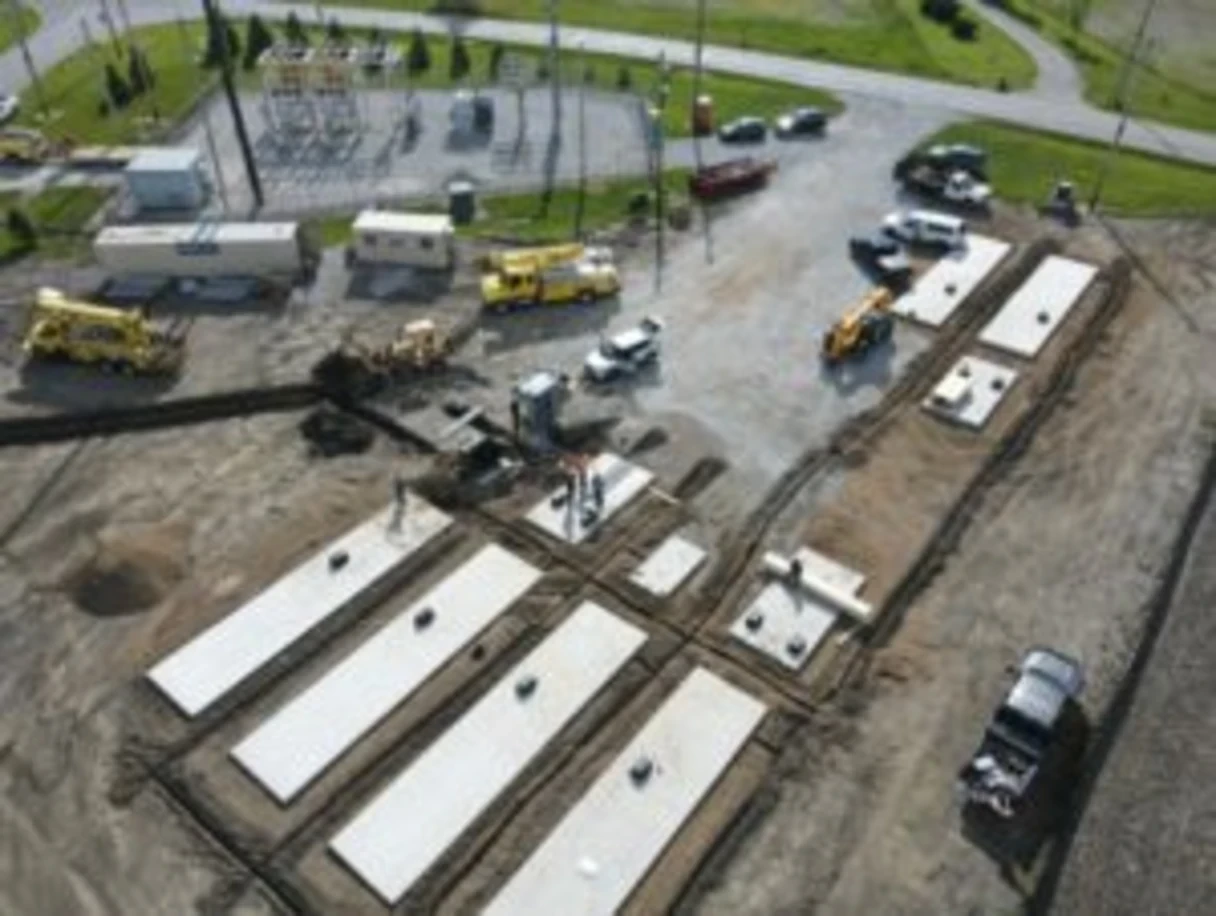
In this view you can see the trenching work happening to lay the lines that will connect the batteries to the substation. The concrete that was poured to form the main pads is curing and we have a good view of the site layout.
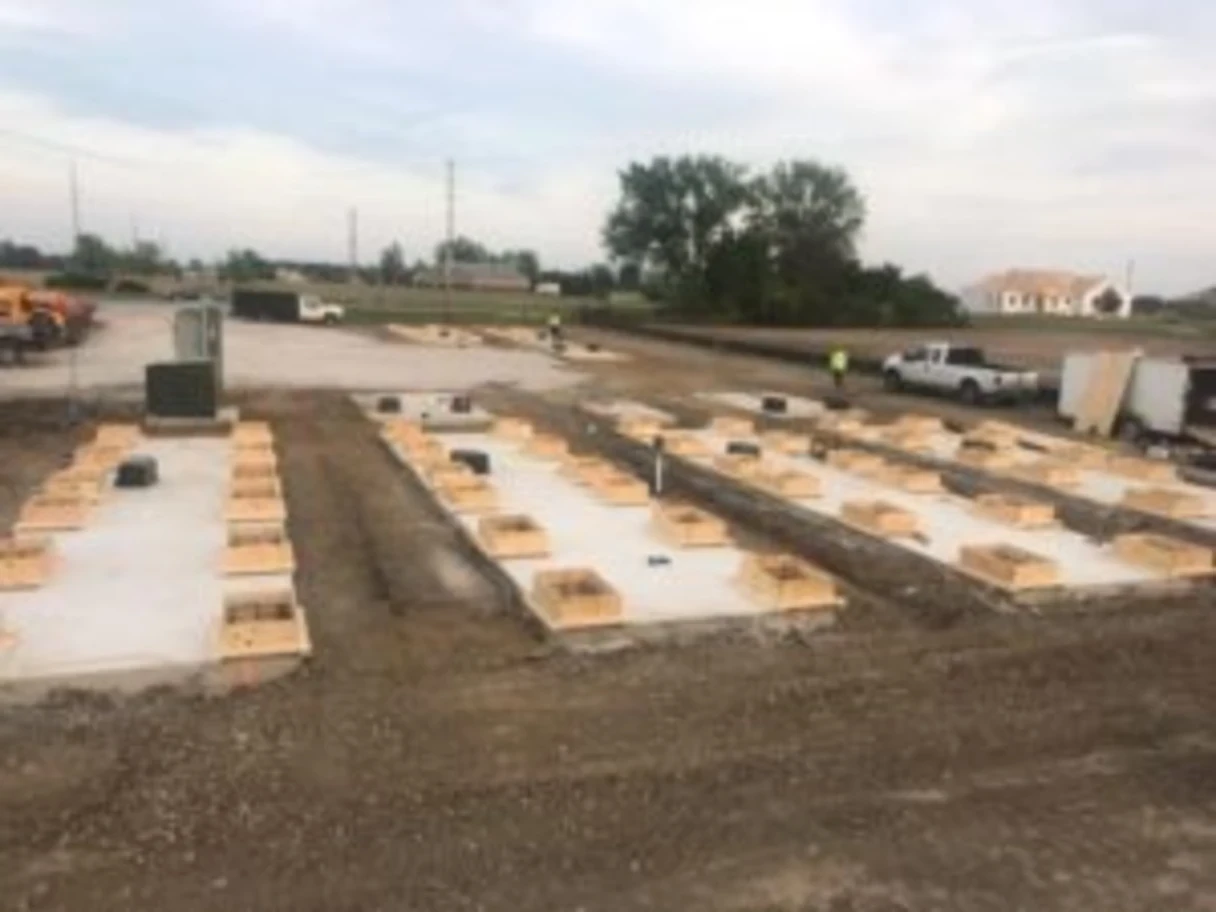
Now that the main pads have cured, you can see the framing boxes for the concrete piers that will get poured next. By lifting the batteries off the main pad, the piers help to dissipate heat from the enclosures and ensure that the batteries aren’t sitting directly in standing water.
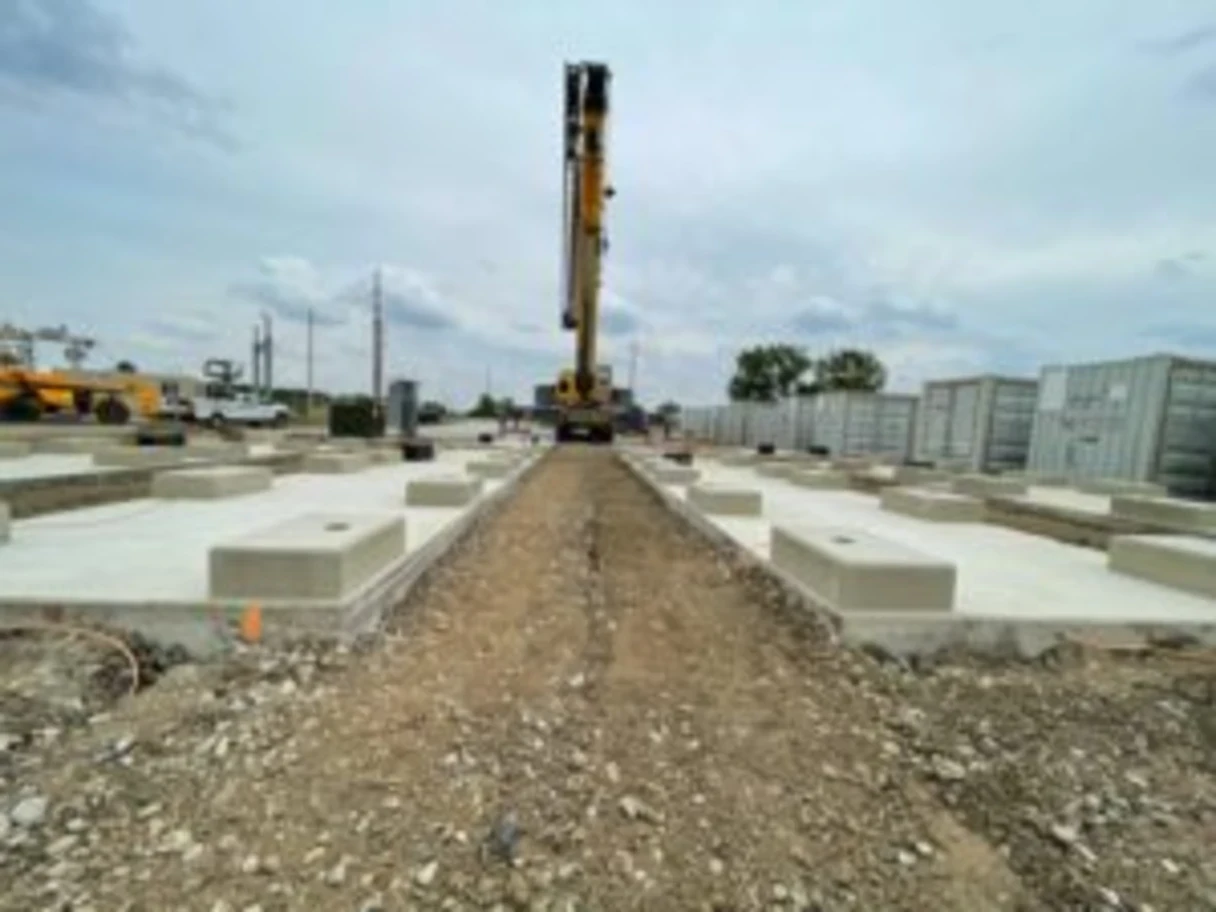
The next step is receiving the major equipment (batteries, power conversion system (PCS) and medium voltage transformers (MVT). You can see our battery enclosure packs on the right after being delivered. The crane in the center is waiting to set them on their piers. Once this step is complete, the electrical work to pull, connect, and terminate cables between the equipment and power source can commence.
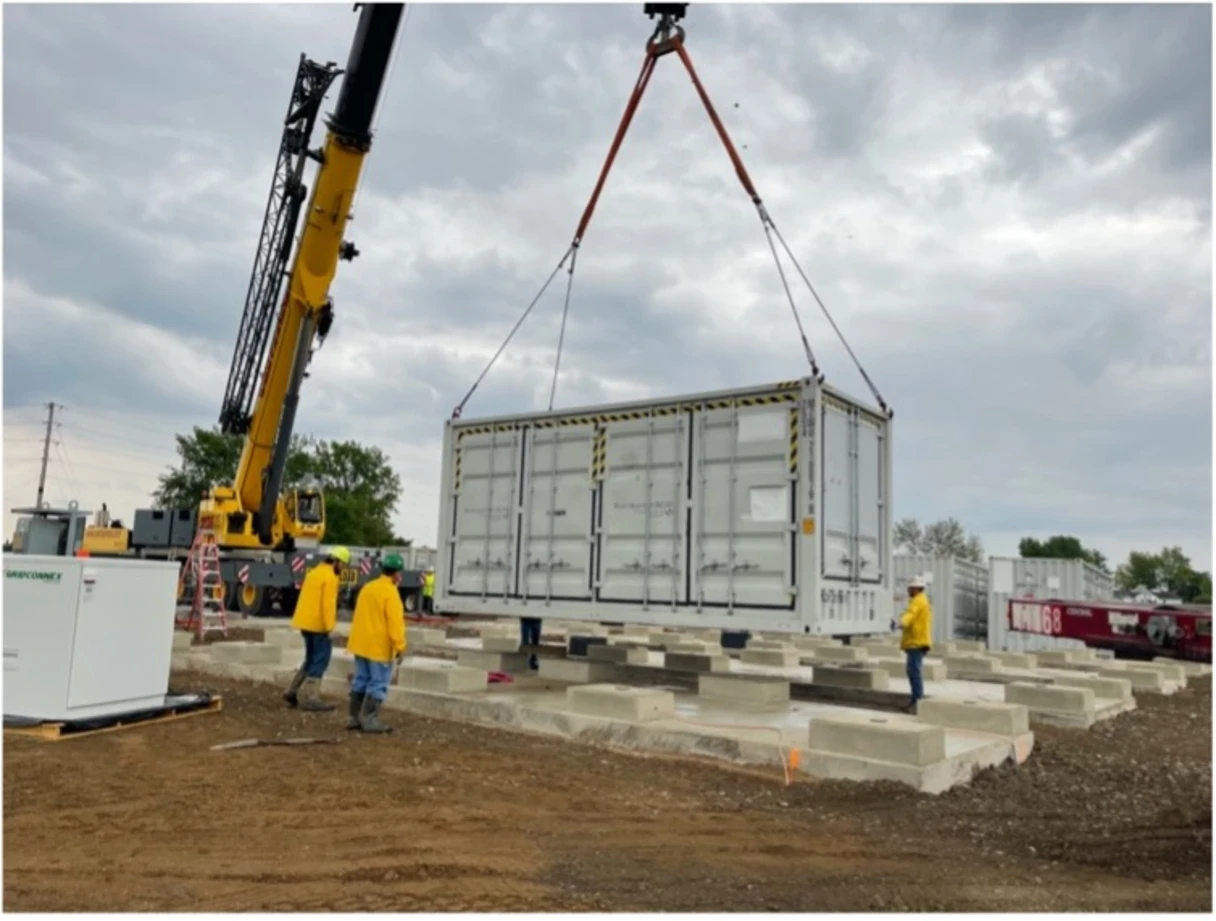
Here’s the exciting part! The crane is lifting the battery pack onto the support piers that are part of the concrete pads. Our crew is there to ensure the batteries are placed squarely on their supports. Once this step is complete, the electrical work to pull, connect and terminate cables between the equipment and power source can commence.
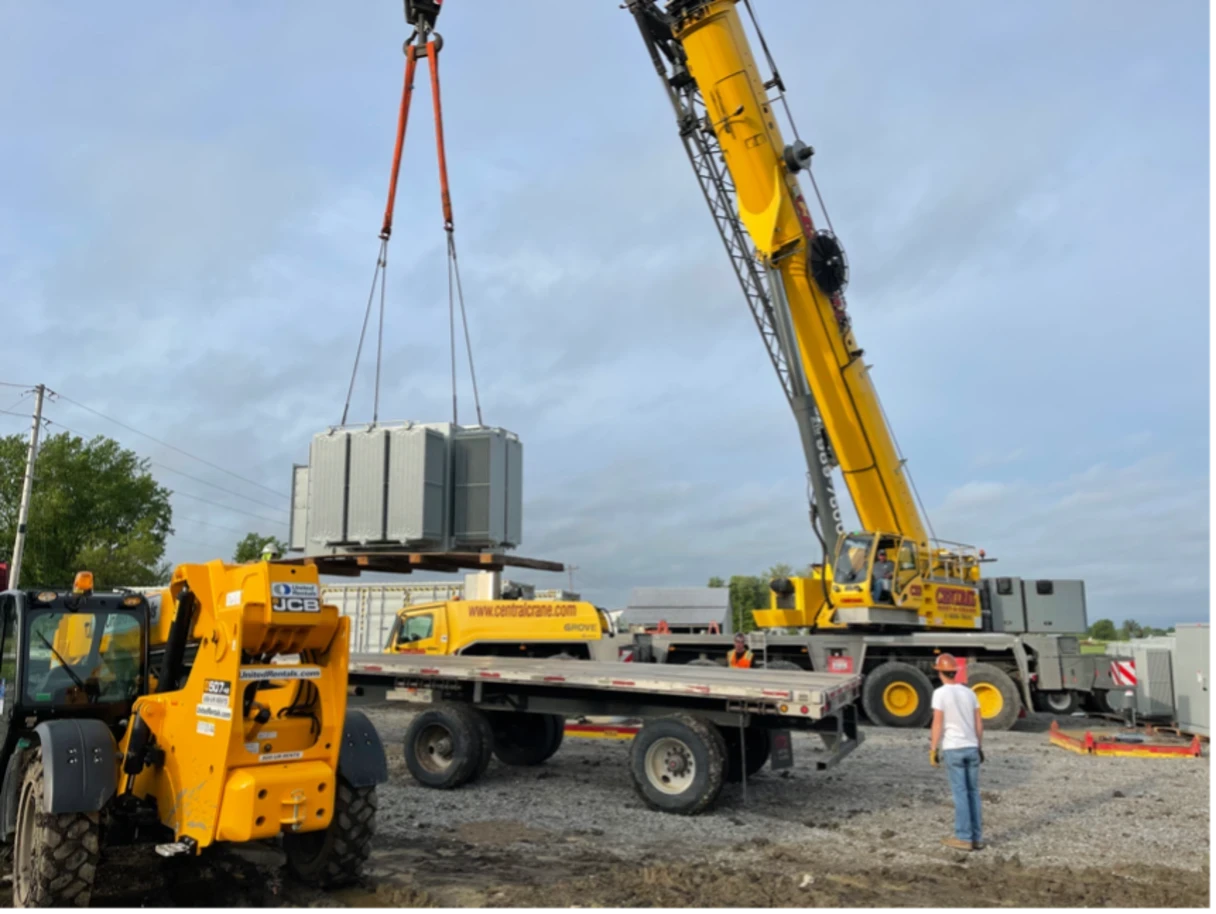
This site needed Medium Voltage Transformers. You can see the crane lifting them off the semi-truck bed to be lowered onto their pads in this photo.
After this is complete, there will be commissioning work done by our engineers (integration and testing) to fully install our Hybrid OS software and make sure it is communicating and operating as designed with the equipment and within the overall system.
At the end of the project, FlexGen typically provides manuals of operation and on-site training to our customers on the use of the software. This is usually scheduled around the close of the project at COD (commercial operation date).
FlexGen offers LTSAs (long term service agreements) to our clients for ongoing maintenance, and monitoring services, which ensures the optimum performance of the system.
*Note: that this breakdown is project specific and there are slight variations in this process for other projects (namely, many require county permitting, public utility paperwork submissions, and interconnection checklists – all of which can add complexity and time to each project).